Fiber Laser Cutters vs. Plasma Cutters: 6 Key Differences
Versatility enables metal fabrication operations to take on a greater variety of work without sacrificing productivity, quality, or time. New computer-controlled metalworking equipment provides precision, speed, and flexibility, so shops can accept a wider range of work.
Along with selecting press brakes and beam coping machines, most shops face a choice of fiber laser cutters vs. plasma cutters. Six key differences can help you determine if you should invest in one or the other, or both, types of machines.
Evolution of Plasma and Laser Cutting Machines
Back in the 1950s, flame cutting was the predominant means of cutting metal; torching metal with fire, generated by fuel with added oxygen, was a common but fairly crude way to cut metal. Although flame cutting could work on thick materials, the range of materials it could cut was limited. It also wasn’t very efficient, taking more time to complete cuts than modern methods. The results often needed further processing, like annealing, to treat heat-affected zones.
Dr. Robert Gage of Union Carbide Industries received the first patent for a plasma cutting machine in 1957. Even before Dr. Gage, Dartmouth researchers James Browning and Merle Thorpe were working on huge plasma torches for NASA to use to simulate re-entry conditions for spacecraft returning home through the atmosphere.
Plasma cutting continued to develop as an efficient way to cut metal. The original enormous torches and machines grew smaller and more manageable, so metal fabrication shops could use them on smaller-scale projects.
Laser cutting came around during the 1960s. Various types of lasers, using gas, crystals, or optical fibers developed nearly simultaneously around 1964. First used to cut diamond dies to draw metal wires, laser cutting developed into a sophisticated and precise way to engrave metal with the help of computer direction. The technique was initially used to cut a wide variety of materials in addition to metal, including leather, wood, plastic, and glass.
Now, even hobbyists have laser cutters to use for engraving and cutting, while metalworking shops use them to produce intricate engraving and cuts on a wide variety of materials.
Amplified Light vs. Electrified Gas
Laser cutters and plasma cutters use different mechanisms to cut. Lasers use optical technology to concentrate and amplify light into a laser beam that is hot enough to melt metal. Laser cutters also use auxiliary gases to blow away the slag or detritus from the cut.
Plasma cutters use electricity to ionize gas to create a superheated stream of plasma that cuts through metal and blows away the melted material, leaving a clean cut.
Materials
Plasma cutters work by causing ionized gas to contact an electrically conducive surface: when the gas hits the metal, it reverts back to its original, non-ionized state. The reaction creates intense heat, which melts the metal, and the gas blows the melted metal away.
But plasma cutters can’t cut wood, which doesn’t conduct electricity, or other non-conductive materials like glass, plastic, or metals that don’t conduct electricity very well, such as tin, lead, or stainless steel.
Plasma cutters are capable of cutting thicker materials; handheld plasma torches can cut up to 1.5 inches, while large industrial machines can cut metal up to 3 inches thick.
Fiber laser cutting machines can cut all types of metal and non-conductive materials, including wood, leather, glass, and plastic. However, they don’t work on reflective metals like copper, brass, or aluminum, as the light can bounce off, thus reducing its power.
It’s also dangerous to use a laser on reflective surfaces because the reflected light can injure people and damage objects. Laser cutters also don’t work well with materials thicker than about half an inch, depending on the type of metal.
Cost
Laser cutters are much more expensive than plasma cutters. But both types of machines have operating costs that include maintenance, parts, safety equipment, energy, and gasses.
Deciding between fiber laser cutters vs. plasma cutters involves more than cost, as metal fabrication shops must also consider the type of work they do.
Tasks and Precision
Laser cutters offer much greater precision than plasma cutters. Lasers also provide a finer and smoother finished cut, while plasma cutters can leave a rougher surface or edge that requires additional finishing.
Lasers can engrave metals with intricate designs without affecting the surrounding area, whereas plasma machines cannot. Lasers can also weld materials together.
While plasma cutting machines cannot weld, they can cut much thicker materials than laser cutters. When you consistently need basic, 2D cutting of thick metals, plasma is the way to go.
Energy Efficiency
Laser cutters are faster than plasma cutters (on thin materials) and use less energy. Plasma cutters, however, can cut through thicker materials that laser cutters would find to be a struggle.
Safety
Both types of cutters present safety concerns, from emitting potentially harmful gasses during the cutting process to dangers to machine operators.
Laser cutting machines may require special enclosures to protect workers from laser light, and plasma cutters can be exceptionally noisy. Plasma cutters also create glare and can emit harmful gasses.
It’s especially important to have proper eye protection when operating a laser cutter, as well as protective clothing that prevents or minimizes burns. Workers also need ear protection from noise, as well as protective shielding or clothing in case of flying debris.
Determine Your Equipment Needs
With fiber laser cutters vs. plasma cutters, six key differences can lead you to the right investment for your specific metal fabrication operation. Consider the materials you work on most often, your clients’ time turnaround expectations, your space limitations, and the costs of running and maintaining your machines.
At Mac-Tech, we can help metalworking shops select the new or previously-owned equipment that best suits their needs. From plasma and laser cutters to press brakes and beam coping machinery, Mac-Tech provides exceptional expertise and superior service. We’ll not only help you choose the right machine, but we’ll also provide preventative maintenance, training, alignment, calibration, and repair services, too.
Check out what our customers are saying about us, and you’ll see that Mac-Tech should be your source for metalworking equipment, service, and repair. Contact us today to discuss your needs, and we’ll help get you up and running and keep you in operation, all with the right equipment for your shop.
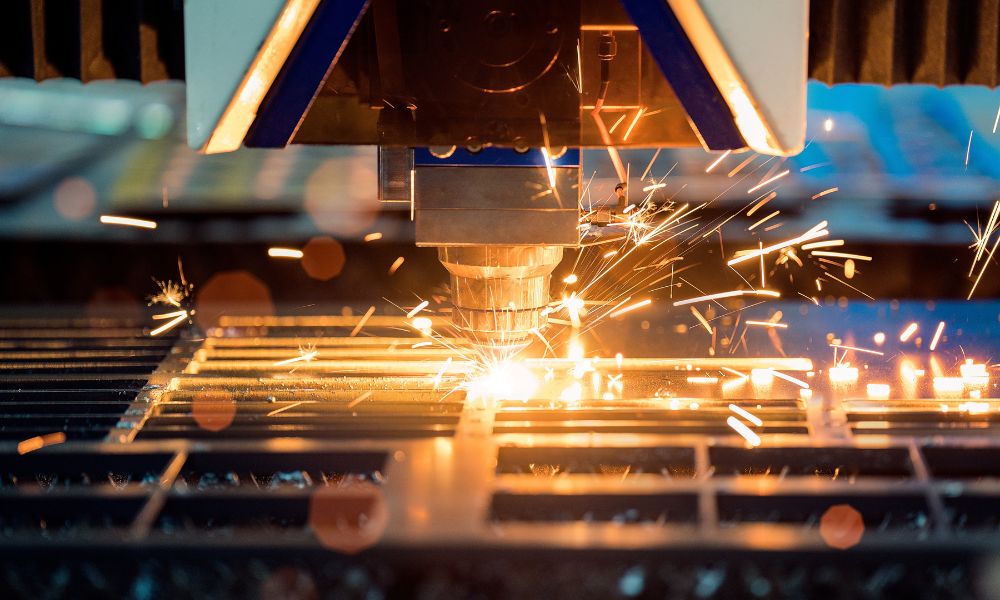